Imagine a world where steel wasn’t as strong, affordable, or widely available as it is today. That’s exactly what life was like before the Bessemer Steel Process came into play. This groundbreaking method transformed the steel industry, making it possible to produce high-quality steel faster and cheaper than ever before. The Bessemer Steel Process didn’t just change manufacturing; it changed history. So, let’s dive into how this process worked, why it mattered, and why it still holds significance today.
Steel has always been a cornerstone of modern civilization, but back in the 19th century, producing it was no easy feat. It was expensive, time-consuming, and labor-intensive. Enter Sir Henry Bessemer, an ingenious inventor who revolutionized the way we think about steel production. His process not only made steel more accessible but also paved the way for industrialization on a massive scale.
But here’s the kicker—the Bessemer Steel Process wasn’t just about making steel cheaper. It was about making it better, stronger, and more efficient. This process allowed manufacturers to produce steel in bulk, which fueled the growth of railways, skyscrapers, and countless other innovations that shaped our world. So, whether you’re a history buff, an engineering enthusiast, or just curious about how things work, this article is for you.
Read also:Legolas Lord Of The Rings Actor Unveiling The Enigma Behind The Elven Archer
Table of Contents
- What is the Bessemer Steel Process?
- A Brief History of the Bessemer Process
- How Does the Bessemer Steel Process Work?
- Advantages and Limitations of the Bessemer Process
- The Impact of the Bessemer Process on Industry
- Comparison with Other Steel Production Methods
- Is the Bessemer Process Still Relevant Today?
- Economic Effects of the Bessemer Process
- Environmental Considerations
- Future Perspectives and Innovations
What is the Bessemer Steel Process?
The Bessemer Steel Process is a method of producing steel by blowing air through molten iron to remove impurities. Developed in the mid-1850s by Sir Henry Bessemer, this process aimed to address the growing demand for high-quality steel during the Industrial Revolution. Before Bessemer’s innovation, steel was produced using labor-intensive methods like puddling or crucible processes, which were slow, costly, and inefficient.
What made the Bessemer Process stand out was its ability to convert large quantities of molten iron into steel in a matter of minutes. By introducing air into the molten iron, carbon and other impurities were oxidized and removed, leaving behind pure steel. This breakthrough not only reduced production costs but also increased output significantly, making steel affordable for widespread use.
Why Was the Bessemer Process a Game-Changer?
Let’s break it down:
- Speed: The process could produce steel in minutes rather than hours.
- Cost: It drastically cut down on the expenses associated with traditional steel production methods.
- Quality: The resulting steel was stronger, more durable, and better suited for industrial applications.
These factors combined to make the Bessemer Steel Process one of the most important inventions of the 19th century.
A Brief History of the Bessemer Process
Sir Henry Bessemer, a British engineer and inventor, patented the Bessemer Process in 1856. At the time, the demand for steel was skyrocketing due to the expansion of railways and the construction of large-scale infrastructure projects. Traditional methods of steel production simply couldn’t keep up with the pace of industrial growth.
Bessemer’s invention wasn’t without its challenges, though. Initially, the process struggled to produce steel from certain types of iron that contained high levels of phosphorus, a common impurity. This limitation led to the development of the Basic Bessemer Process, which used a lining of basic materials to neutralize phosphorus and improve the quality of the steel.
Read also:Dilbert Comics A Mustread For Every Office Worker Looking To Survive The Madness
Key Milestones in the Development of the Process
Here’s a quick timeline:
- 1856: Sir Henry Bessemer patents the original process.
- 1878: The Basic Bessemer Process is introduced to handle phosphorus-rich iron.
- 1890s: The process reaches its peak popularity before being phased out by newer technologies.
Despite its eventual decline, the Bessemer Process laid the foundation for modern steel production techniques.
How Does the Bessemer Steel Process Work?
The Bessemer Steel Process involves several key steps:
- Melting the Iron: Raw iron is melted in a furnace until it becomes molten.
- Blowing Air: Air is forced through the molten iron, causing impurities like carbon and silicon to oxidize and escape as gases.
- Adding Flux: Limestone or another flux material is added to help remove additional impurities.
- Casting the Steel: Once the impurities are removed, the resulting steel is poured into molds for cooling and solidification.
While the process may sound simple, its efficiency and effectiveness were revolutionary at the time. By removing impurities quickly and efficiently, the Bessemer Process ensured that the resulting steel was of high quality and suitable for a wide range of applications.
Tools and Equipment Used in the Process
Some of the essential tools and equipment include:
- Bessemer Converter: A large vessel used to contain the molten iron and blow air through it.
- Furnaces: Used to melt the raw iron before the conversion process.
- Flux Materials: Substances like limestone that help remove impurities during the process.
Advantages and Limitations of the Bessemer Process
Like any groundbreaking invention, the Bessemer Steel Process had its pros and cons. Here’s a closer look:
Advantages
- Cost-Effective: The process significantly reduced the cost of steel production.
- High Output: It allowed for the mass production of steel, meeting the demands of industrialization.
- Improved Quality: The resulting steel was stronger and more durable than that produced by earlier methods.
Limitations
- Phosphorus Issue: The original process struggled with iron containing high levels of phosphorus, leading to the development of the Basic Bessemer Process.
- Environmental Concerns: The process released large amounts of carbon dioxide and other pollutants into the atmosphere.
- Material Restrictions: It was only effective for specific types of iron, limiting its versatility.
The Impact of the Bessemer Process on Industry
The Bessemer Steel Process had a profound impact on various industries, particularly in the fields of transportation, construction, and manufacturing. Here’s how:
Railway Expansion
Steel produced through the Bessemer Process was used extensively in the construction of railways. Its strength and durability made it ideal for building tracks, bridges, and locomotives, facilitating the rapid expansion of rail networks across the globe.
Skyscraper Construction
As cities grew, so did the demand for tall buildings. The availability of affordable, high-quality steel made it possible to construct skyscrapers, revolutionizing urban architecture.
Manufacturing Growth
From machinery to household goods, the Bessemer Process enabled manufacturers to produce steel products more efficiently and at a lower cost, driving economic growth and innovation.
Comparison with Other Steel Production Methods
While the Bessemer Process was revolutionary, it wasn’t the only method of producing steel. Here’s how it stacks up against some of its competitors:
Puddling Process
This older method involved heating and stirring molten iron to remove impurities. However, it was slow, labor-intensive, and expensive, making it less practical for large-scale production.
Open Hearth Process
Developed later, the Open Hearth Process offered greater flexibility and control over the chemical composition of the steel. It could handle a wider range of materials and produce higher-quality steel than the Bessemer Process.
Basic Oxygen Furnace
This modern method uses pure oxygen instead of air to remove impurities, resulting in even faster and more efficient steel production. It eventually replaced the Bessemer Process as the dominant method in the steel industry.
Is the Bessemer Process Still Relevant Today?
While the Bessemer Process has largely been replaced by more advanced technologies, its legacy lives on. It paved the way for modern steel production methods and demonstrated the importance of innovation in meeting industrial demands. Today, engineers continue to build upon the principles established by Bessemer, striving for more efficient, sustainable, and cost-effective ways to produce steel.
Lessons Learned from the Bessemer Process
Here are a few takeaways:
- Innovation drives progress in industry and beyond.
- Efficiency and cost-effectiveness are key to widespread adoption of new technologies.
- Environmental considerations must be factored into modern manufacturing processes.
Economic Effects of the Bessemer Process
The economic impact of the Bessemer Steel Process cannot be overstated. By reducing the cost of steel production, it made steel accessible to a broader range of industries and consumers. This affordability fueled industrial growth, created jobs, and stimulated economic development worldwide.
Moreover, the process spurred innovation in related fields, leading to the development of new technologies and methods that further enhanced productivity and efficiency.
Global Economic Benefits
From the United States to Europe and beyond, countries that adopted the Bessemer Process experienced significant economic growth. The availability of affordable steel enabled the construction of infrastructure, the expansion of industries, and the improvement of living standards for millions of people.
Environmental Considerations
While the Bessemer Process revolutionized steel production, it also raised environmental concerns. The large-scale release of carbon dioxide and other pollutants into the atmosphere contributed to air pollution and climate change. As awareness of these issues grew, the industry began exploring cleaner, more sustainable alternatives.
Modern steel production methods prioritize environmental responsibility, incorporating technologies that minimize emissions and reduce the overall environmental footprint of steel manufacturing.
Future Perspectives and Innovations
Looking ahead, the steel industry continues to evolve, driven by the need for sustainability, efficiency, and innovation. Researchers are exploring new methods of steel production that reduce energy consumption and emissions while maintaining or improving quality.
Technologies such as electric arc furnaces, direct reduced iron processes, and hydrogen-based steelmaking offer promising solutions for a more sustainable future. By building on the lessons of the past, the industry can continue to meet the demands of a growing world while minimizing its impact on the environment.
Key Innovations to Watch
- Electric Arc Furnaces: Use electricity to melt scrap steel, reducing energy consumption and emissions.
- Hydrogen-Based Steelmaking: Replaces carbon with hydrogen as a reducing agent, eliminating carbon dioxide emissions.
- Recycling Technologies: Focus on maximizing the use of recycled materials in steel production.
Conclusion
The Bessemer Steel Process was more than just a method of producing steel—it was a catalyst for industrial progress and economic growth. By making steel faster, cheaper, and better, it transformed industries, fueled innovation, and shaped the modern world. While newer technologies have largely replaced it, the principles and lessons of the Bessemer Process continue to inspire advancements in steel production today.
So, what’s next? As the industry moves toward a more sustainable future, the legacy of the Bessemer Process serves as a reminder of the power of innovation and the importance
:max_bytes(150000):strip_icc()/Bessemer-process01-3000-3x2gty-58b4e7c75f9b586046963aff.jpg)
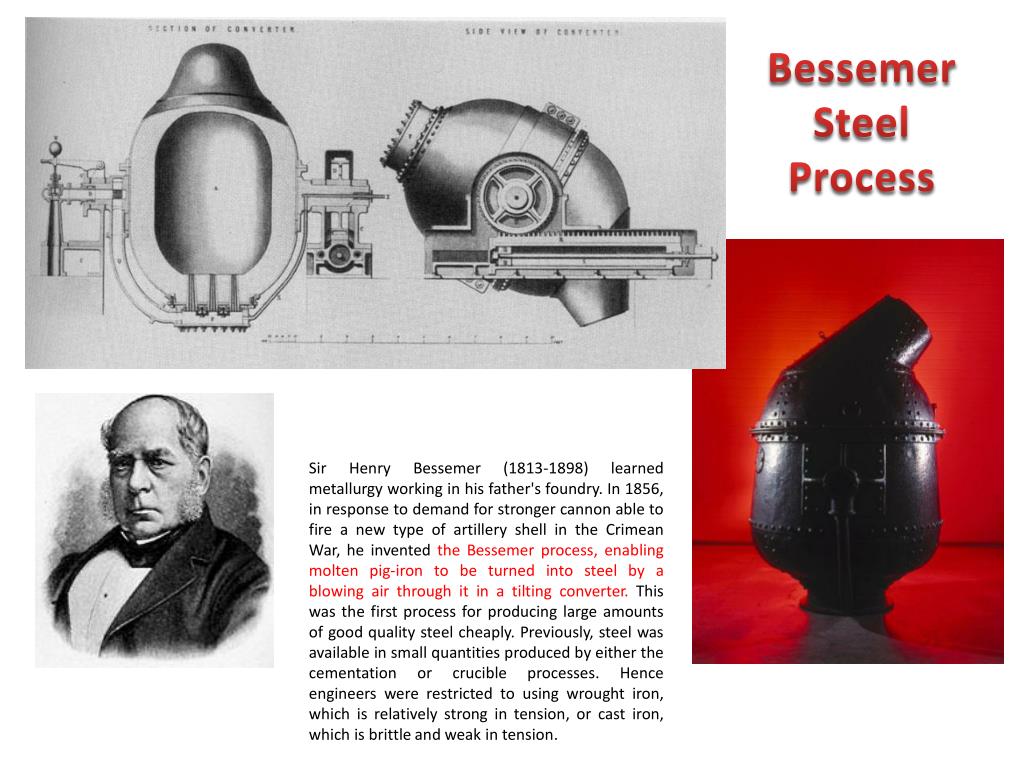
